The New Frontier: Opportunities In Manufacturing 4.0 & Beyond
First in a three-part series decoding the next wave of opportunities in Manufacturing Tech
The New Frontier: Opportunities In Manufacturing 4.0 & Beyond
First in a three-part series decoding the next wave of opportunities in Manufacturing Tech
Manufacturing technology, a sector we strongly believe is brimming with promise and potential, is typically overlooked by aspiring founders as the startup world continues to expand. Some cutting-edge technologies that are today revolutionizing manufacturing processes seemed inconceivable not too long ago. The result is an industry that is faster, cheaper, and more efficient than ever before. In this three-part article series, we turn the spotlight on technology solutions for manufacturing and provide compelling reasons why this area deserves to be high on the priority list for builders.
The manufacturing industry is currently undergoing a rapid transformation, fueled by innovations in Internet of Things (IoT), Artificial Intelligence (AI), Machine Learning (ML), Computer-Aided Design (CAD), 3D printing, edge computing, etc., as well the regulatory landscape and public sentiments around the ecosystem.
By 2030, companies developing solutions for the manufacturing sector could generate an economic value between $2.5 trillion and $4 trillion. In other words, the manufacturing industry is primed for disruption, and you don't want to miss out.
In this blog series, we'll delve into Manufacturing 4.0 and beyond, examining the driving forces behind the growth of Manufacturing 4.0 solutions, the key enablers in the field, the primary manufacturing categories undergoing transformation, and the anticipated tailwinds for this sector. We will also explore the emerging concept of Manufacturing 5.0, its key drivers and considerations behind the concept, its implications on the emerging technology and processes, and how it is set to shape the future of manufacturing.
But before we get into all that, let's take a step back to understand how manufacturing has evolved over the last two centuries.
The Evolution Of Manufacturing Technology
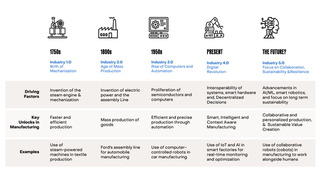
The evolution of manufacturing technology can be traced back to the First Industrial Revolution or Industry 1.0, which started in the late 18th century. The key innovation in this era was the development of mechanization and the introduction of steam and water power. This led to the creation of factories.
Industry 2.0 or the Second Industrial Revolution, started in the late 19th century due to the emergence of new power sources like electricity, oil, and gas. Electricity enabled machines to operate more efficiently, and inventions like the assembly line facilitated the mass production of various products, such as automobiles.
Industry 3.0, also known as the Third Industrial Revolution, started in the 1960s with the introduction of computerization and automation. This allowed for greater precision and accuracy in manufacturing, and led to the creation of more complex products such as circuit boards, computer chips, telecom devices, and other precision components.
Industry 4.0 is the current phase of the industrial revolution and is characterized by the introduction of smart, cyber-physical systems into the manufacturing process. This includes the use of technologies such as the Internet of Things (IoT), AI/ML, and big data analytics. These technologies enable the collection and analysis of vast amounts of data, which can be used to optimize production processes, forecast operational inefficiencies, reduce waste, and increase productivity. Each phase of the industrial revolution has built upon the innovations of the previous phase, leading to greater automation, precision, and control in manufacturing processes. And Manufacturing 4.0, a subset of Industry 4.0, represents a new era of manufacturing, where companies use the power of data and smart computing to create a network of machine systems to help optimize production.
As we look toward the future, with open questions on human contribution in the wake of absolute automation, the emerging concept of Industry 5.0 or the Fifth Industrial Revolution is beginning to take shape and will also affect the manufacturing ecosystem. Manufacturing 5.0 signals the paradigm shift from automation-centric processes to a collaborative ecosystem where humans and machines coexist and complement each other. This evolution is characterized by a combination of cyber-physical systems with human intellect and aims to foster a more personalized and sustainable manufacturing landscape. Rather than replacing human labor with machines, Manufacturing 5.0 envisions a synergistic workspace where human creativity and machine efficiency combine to enhance overall productivity, leveraging the strengths of both.
Recapping The Advances Leading To Manufacturing 4.0
Manufacturing 4.0 signifies the evolution of manufacturing processes through the adoption of advanced technologies like automation, artificial intelligence, machine learning, cloud computing, etc. By gathering and analyzing vast amounts of data, these technologies empower companies with insights that help them identify performance issues in real time, optimize production processes, ensure compliance with government safety regulations, and automate tasks that lead to improved speed and efficiency.
Several factors have led to the emergence of Manufacturing 4.0 as a key area of focus for startups and established players in the manufacturing industry. These include:
- Shift towards automation: The need to reduce costs, improve efficiency, and increase productivity has led to a shift toward automation in manufacturing. Robotic process automation (RPA) and other automated systems have led to a reduction in labor costs and improved safety for workers, leaving companies wanting more.
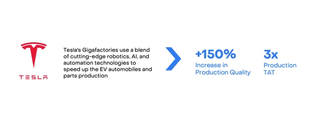
- Increased data capture: The availability of IoT sensors and other data capture technologies have enabled manufacturers to collect vast amounts of data about their processes and products. This data has the potential to optimize production processes, improve product quality, and reduce downtime.
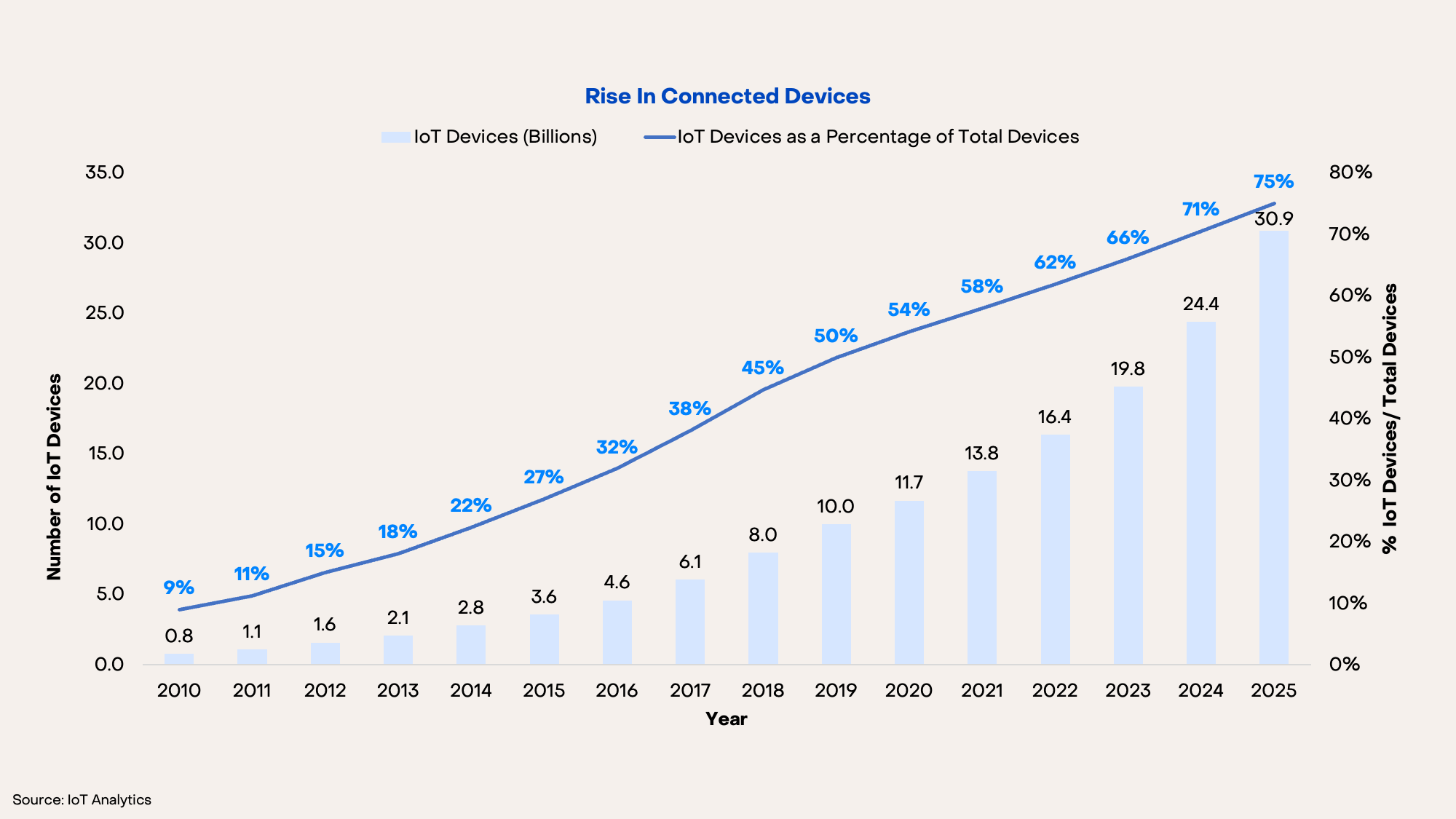%20(1).png?w=320&h=180&auto=format)
- Complex processes: The rise of devices being tracked, along with the increasing complexity of manufacturing processes across all these systems, leads to a lot of downtime and other operational inefficiencies. Most experts estimate that the industry loses almost $1 trillion in downtime-related inefficiencies and productivity losses.
- Regulatory pushes: Government regulations and mandates, such as environmental regulations and safety standards, have also played a role in the adoption of Manufacturing 4.0 & 5.0 technologies. With increasing concerns around environmental degradation, worker safety & health, and cybersecurity failures, governments have enacted various acts and introduced laws to provide more robust guardrails for the future of sustainable and responsible manufacturing.
- Internet of Things Cybersecurity Improvement Act,
- Occupational Safety and Health Administration (OSHA) regulations,
- Fair Labor Standards Act (FLSA),
- Network and Information Security (NIS) Directive
- Registration, Evaluation, Authorisation, and Restriction of Chemicals (REACH)
- ISO 14000 series
These factors have created an opportunity for new companies to take the sector by storm. The last five years have seen a huge increase in the number of startups in the Manufacturing space, and most of this would not be possible without the below technological advances.
Key Tech Drivers That Led To The Success Of Manufacturing Tech
Computational power and connectivity: High-speed network connectivity and exponential growth in computing power have given us the ability to collect manufacturing data from various plants and processes in real-time and analyze them for insights. This has led to the development of several cloud-based manufacturing solutions that can help you optimize production processes across all your manufacturing plants from a single location.
In April just this year, Snowflake launched their Snowflake Manufacturing Data Cloud to help manufacturers and suppliers with access to resources that enable them to manage supply chains, enhance shop floor efficiencies, and offer better products/services to customers.
AI/ML: The dawn of AI and machine learning systems have been helpful in predictive maintenance, quality control, and supply chain optimization. AI/ML algorithms can find patterns and anomalies in real-time, and help manufacturers make data-driven decisions.
GE Transportation, a division of General Electric (GE), employs AI/ML technologies to carry out predictive maintenance of locomotives. Their proprietary AlertTM technology offers real-time status of locomotive health and performance. By delivering instantaneous health assessments and diagnostics for essential locomotive components, the system facilitates proactive planning for maintenance schedules, parts, and the allocation of resources.
Human-machine interface: The use of advanced sensors, augmented reality, and wearables have enabled workers to interact with machines and systems like never before. This is changing the way R&D is done in manufacturing companies. Virtual design and walkthroughs have made it easier to make a working prototype, as they can be made before you can build them in real life.
Modern production methods: Modern prototyping technologies, like 3D printing, have enabled the production of complex shapes and parts that were previously impossible to produce. This has reduced lead times and costs, and enabled mass customization. In addition, digital twins – virtual replicas of physical assets – have enabled manufacturers to simulate and optimize production processes before implementing them in the real world.
Breaking Down The Manufacturing Tech Landscape In The 4.0+ Era
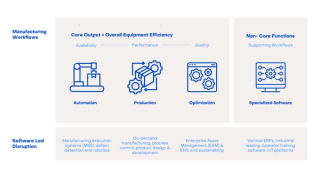
New startups are disrupting the traditional manufacturing sector in the following categories: production, automation, optimization, and specialized software. Let's take a closer look at each of these categories and their role in transforming the manufacturing industry.
- Production: On-demand manufacturing, process control, and product design & development are some areas where startups are building new solutions.With on-demand manufacturing, companies can produce custom products quickly and efficiently, reducing inventory costs and improving overall responsiveness to customer needs. Process control technology helps to improve the quality and consistency of manufactured goods, while product design and development tools enable companies to create and test new products faster and more efficiently.
- 549 startups working in this category have received total funding of $1.8 billion over the past 24 months.
- Automation: Manufacturing execution systems (MES) and robotics are two key areas where startups are making significant strides.MES technology allows manufacturers to track production processes in real time, optimizing production efficiency and reducing waste. Robotics, on the other hand, is being used to automate many repetitive and dangerous tasks, improving worker safety and increasing productivity.
- 405 startups working in this category have received funding of $2.2 billion over the past 24 months.
- Optimization: Enterprise Asset Management (EAM), Environment, Health & Safety (EHS), and sustainability are three critical areas where startups are focusing their efforts. EAM technology helps manufacturers create digital twins, optimize their asset utilization, extending the life of equipment and reducing maintenance costs. EHS tools enable companies to monitor and manage environmental and workplace safety risks effectively, while sustainability software helps manufacturers reduce their carbon footprint and meet their sustainability goals.
- 357 startups working in this category have received a funding of $784 million over the past 24 months.
- Specialized software: ERP and CRM systems, Manufacturing IoT, and workforce management are some specialized software solutions that startups are building.ERP and CRM systems help manufacturers manage their business operations more efficiently, streamlining processes from procurement to sales. Manufacturing IoT, on the other hand, provides real-time visibility into manufacturing processes, allowing companies to make data-driven decisions that optimize production. Finally, workforce management software helps manufacturers manage employee schedules, track attendance, and automate HR processes.
- 246 startups working in this category have received a funding of $1.2 billion over the past 24 months.
By understanding the key categories within the Manufacturing landscape, founders can identify opportunities for innovation and growth in this exciting and rapidly evolving space.
Why The Fifth Industrial Revolution?
The rise of machine-led automation and the industry’s increasing impact on the environment and society has caused a shift in focus from mere monetary value to broader societal value. The Fifth Industrial Revolution, which is beginning to take shape, represents a shift from the focus on automation and technology to a focus on collaboration between humans and machines, with the following core principles:
- Collaboration: Focus on the collaboration between humans and machines, with machines designed to assist and augment human capabilities rather than replace them.
- Personalization: The ability to cater to individual needs and provide personalized products and services.
- Sustainability: A focus on creating systems that are sustainable and have minimal impact on the environment.
- Value Creation: The aim is to create new forms of value that balance people, planet, and prosperity
- Adaptability: Agile manufacturing ecosystems to quickly adapt adverse situations like Covid-19 or other natural/manmade mishaps
For the next generation of manufacturing tech companies, Industry 5.0 presents a new set of opportunities and challenges. On one hand, it opens up the potential for creating more personalized products and services, as the collaboration between humans and machines allows for greater customization and flexibility in the manufacturing process. On the other hand, it also requires a shift in mindset and approach, as companies will need to design their systems and processes with human-machine collaboration in mind. This could involve the use of technologies such as augmented reality for training and guidance, AI and machine learning for decision support, and advanced robotics that can work safely alongside humans in a sustainable and eco-friendly manner.
In our next blog post in the series, we'll dive into the exciting world of Manufacturing Tech, highlighting important categories and uncovering growth opportunities. We'll talk about decision-makers, user personas, and what drives their choice of manufacturing 4.0 & 5.0 solutions. Additionally, we'll explore the sub-categories and their various applications, and take a look at the investment landscape and success stories in this booming market.
If you are building in this space or deeply interested in it, we’d love to hear from you. Do reach out to us.
Written by Poorvi Vijay
Related
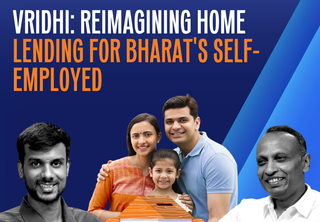
Vridhi: Reimagining Home Lending For Bharat's Self-Employed
Ram Naresh Sunku, Co-founder, Vridhi Home Finance
11.12.2024
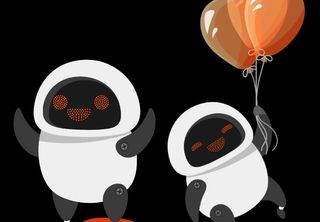
Investing in Plena Data
Automating manual accounting tasks and improving employee experience with robots
14.10.2021

Monetization Strategies That Work: Insights from Consumer Tech Founders
Insights on what works when it comes to monetizing consumer apps in India.
10.12.2024